top of page
See FISITA Library items from Hyundai Motor Group
F2021-CAF-028
Paper + Video
Dipl.-Ing. Jinseok Chang, Hyundai Motor Group, REPUBLIC OF KOREA
Mr. Minjae Kim, Hyundai Motor Group, REPUBLIC OF KOREA
Dr.-Ing. Dae Choi, Hyundai Motor Group, REPUBLIC OF KOREA
Dipl.-Ing. Yongseok Kang, Hyundai Motor Group, REPUBLIC OF KOREA
Detail
The new 3L diesel engine for passenger cars has been developed as the highly-performing and environment-friendly 3rd generation engine of Hyundai Motor Group. It is the newly-developed inline – 6 cylinders 3.0L diesel engine, and its performance for power, fuel efficiency, NVH, and responsiveness has been optimized for the first SUV of the GENESIS brand, GV80 - Project code: JX1.
The future trend of powertrain is that although electrification and hybridization are continuously increasing, the internal combustion engine is still expected to play a role as a powertrain with sufficient production volume even in the future after 2030.
This engine is equipped with an aluminum block, a common rail of pressure 2200 bar, a ball bearing turbocharger, a water-cooled intercooler, an LP(Low Pressure) & HP (High Pressure) EGR system, and has an LNT, a DPF , and an SCR as after-treatment devices.
The combustion system of this engine was newly developed in common with HMG’s new diesel 2.0, 2.2, and 3.0L module engines. The combustion chamber has been improved in shape and spray compared to HMG’s previous V6 3L engine. And configuration of Injector nozzle, NTP, and valve timing have been optimized for the new combustion chamber. The turbo-charger has also been newly optimized for the power, fuel efficiency and responsiveness of the new engine. Accordingly, the responsiveness of the engine has been remarkably improved compared to the previous engine, and the power performance of the vehicle has also been improved very well.
The performance of the intake manifold was also improved through several times with focus on air and EGR distribution, and also on cost, weight reduction, and robustness.
The back pressure level of the exhaust system was developed in consideration of both power and NVH performance with focus on the GENESIS brand. In consideration of this, the engine's NVH showed better results than the engines of the previous HMG’s and competitors.
Its maximum power advanced 7% more than the previous HMG’s engine, and it has also become a 3L diesel engine with the highest power, overtaking competitors.
The engine's fuel efficiency is improved by about 6% over the previous HMG's engine. In addition, the results were 5-10% better than competitors' engines, and vehicle fuel efficiency was 13% superior to the previous HMG’s and 8-9% superior to competitors. Through this, it has secured the world's best fuel efficiency and power performance competitiveness.
For the after-treatment devices, the EMS mapping development of the exhaust heating was efficiently progressed according to the state of the after-treatment devices, and the water-cooled intercooler and the complex EGR system were developed to operate properly including the extended RDE at low temperature. The SCR system showed a high NOx conversion efficiency of over 80% in regulatory modes such as WLTC and RDE STEP2.
The new 3L diesel engine’s performance accords with the world-best-class fuel efficiency and high-performance for the world-premium brand GENESIS, satisfying with the latest environmental regulation EURO6d.
FISITA World Congress 2021
CAF - Conventional and Alternative Fuels and Lubricants
Downloads
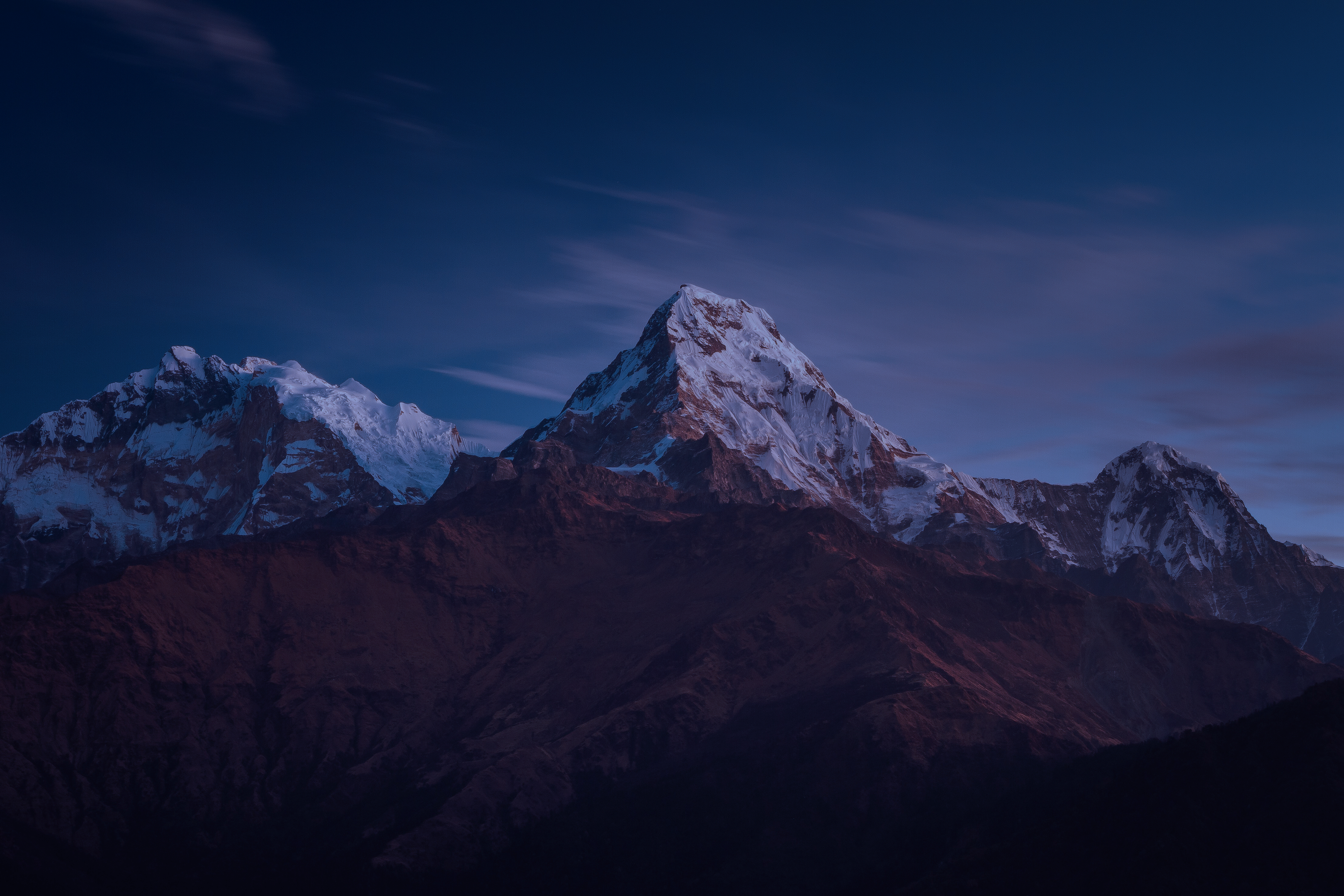
F2020-MML-003
Paper + Video
Mr. JIYONG LEE, HYUNDAI MOTOR GROUP, REPUBLIC OF KOREA
Mr. CHEOLUNG LEE, HYUNDAI MOTOR GROUP, REPUBLIC OF KOREA
Detail
The most commonly used casting technique for the manufacture of aluminum parts in automobiles is the HPDC(High Pressure Diecasting) process. This process is a trend that automotive companies continue to increase the application of HPDC because cycle time of HPDC is much shorter than conventional casting methods such as gravity casting process and low pressure casting process. for this reason HPDC can lower manufacturing costs.
However, HPDC has one fatal disadvantage. When there are complex flow paths and undercut shapes inside such as water pump housings and cylinder heads, this internal geometry cannot be implemented by HPDC, so the product is forced to be manufactured using low-pressure casting process or gravity casting process that are low in productivity but can implement internal geometry through the sand core. In general, low pressure casting process and gravity casting process are 30 to 50% more expensive to manufacture than HPDC.
In order to overcome these shortcomings, this paper had researched "Salt Core Technology" that can be used in HPDC process. Salt core technology is considered to be the core technology that enables undercut shape to be applied to HPDC process, can replace gravity casting part which has undercut shape. Also, It can reduce the aluminum part weight up to 10% through reducing the wall thickness. Moreover, it can reduce the part cost around 10 to 15% through productivity improvement and using cheap aluminum alloy. Salt core shall have high strength to overcome 800bar in HPDC, but shall have low strength in decoring. In this study, we studied the recipes of salt core that can implement these characteristics.
Through this study, Hyundai Motor Group has succeeded in mass production by applying Salt Core technology to aluminum parts and expects this technology to spread to other industries. The strength of the developed salt core is 15MPa or higher and is designed to withstand the high pressure of the high-pressure casting process. Using this research result, Hyundai Motor succeeded in mass production by applying Salt Core to aluminum parts.
FISITA World Congress 2021
MML - Manufacturing, Materials and Lightweight Solutions
Downloads
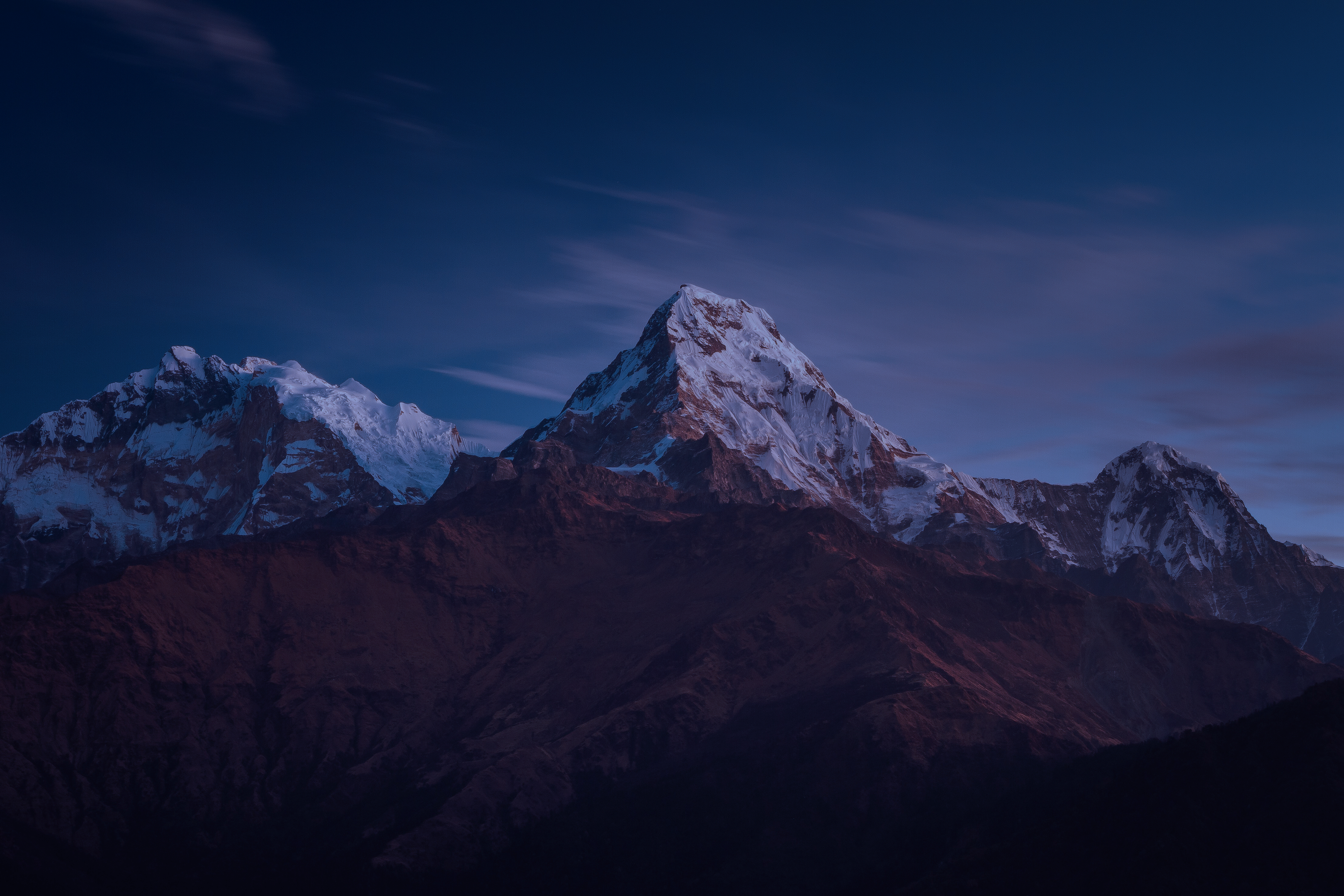
Error message goes here.
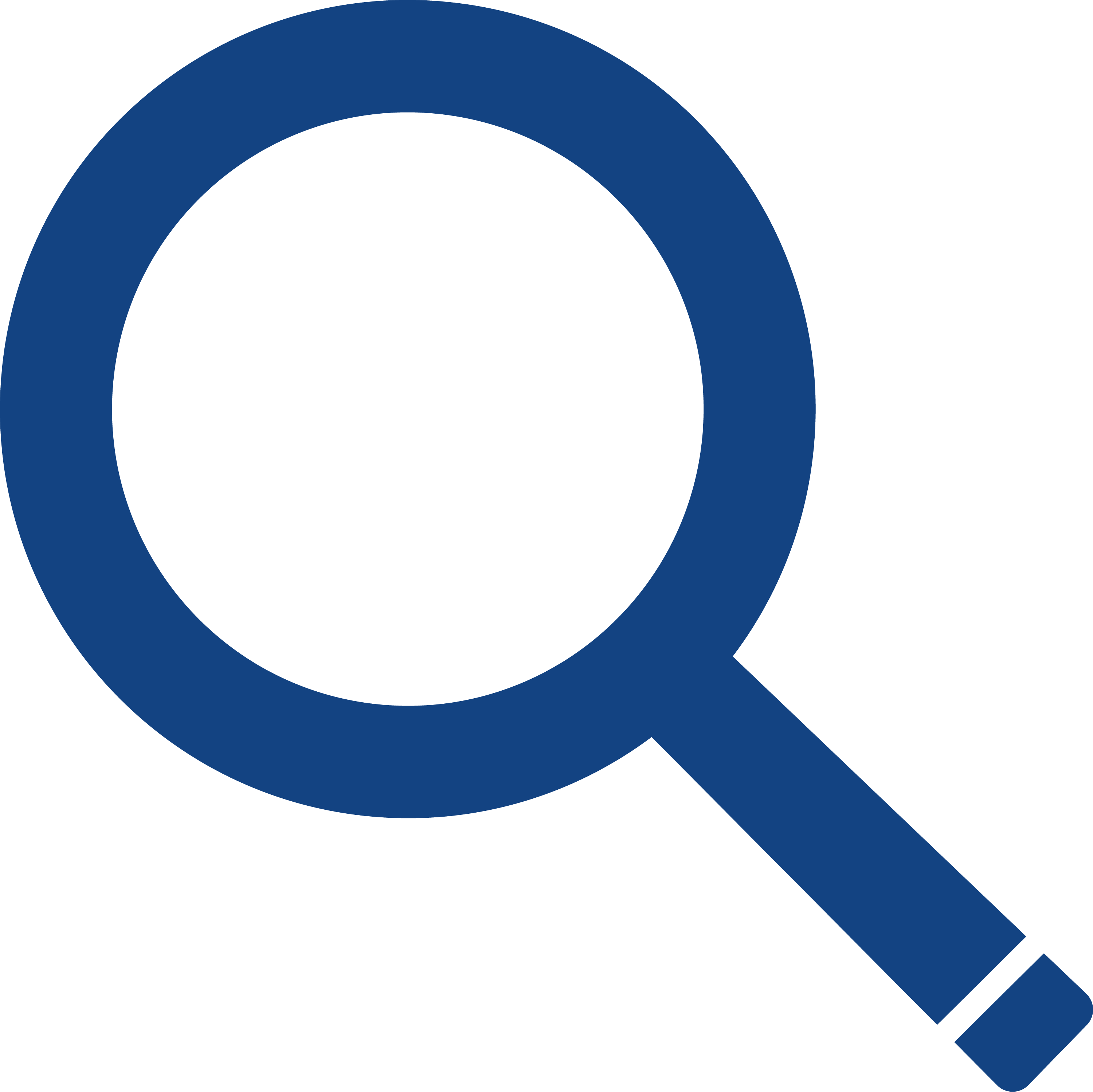
bottom of page