See FISITA Library items from Dilek Bayrak Akça
EB2020-STP-005
Paper + Poster + Pitch
Abstract
Ms. Dilek Bayrak Akça, Ford Otosan, TURKEY
Ms. Öznur Çetin, Ford Otosan, TURKEY
Dipl.-Ing. Yasin Hacısalihoğlu, Ford Otosan, TURKEY
Dr.-Ing. Ibrahim Can Guleryüz, Ege Fren, TURKEY
Dipl.-Ing. Barış Yılmaz, Ege Fren, TURKEY
Brake Rotor Vane Modification Effect in the Enhancement of Heat Transfer for Heavy Duty Vehicles
Nowadays, vehicle manufacturers are straggling with hard environmental requirements consistently. CO2 reduction and friction material emissions are the most important concerns highly considered by governments. Weight is the key parameter of the vehicle design due to its effects on both fuel consumption and CO2 emission. There is a trade-off between brake rotor’s thermal capacity and weight. Decreasing brake rotor weight reduces thermal capacity and it decreases braking performance of the vehicle because of sudden temperature increase above the material’s maximum operating temperature.
Ventilated brake rotors are in use for long haul tractors due to increase in surface area of heat transfer and reduction in mass of rotor. Also, improving cooling performance of brake rotor may reduce the wear of pad and rotor. The generated heat during braking is rejected to surrounding mainly by forced convection. It is clear that failure of brake rotor is due to high thermal stresses developed by large temperature gradient between friction surfaces and ventilation vanes of the rotor. Pillared rotors are alternative to radial vane rotors as they have more uniform temperature distribution within rotor passages. Even though mass flow rate in case of pillared rotors is less than radial type rotors, the rate of heat transfer on vehicle level are found to be similar in both cases.
Computational fluid dynamics (CFD) is used to determine cooling performance of ventilated brake rotors on both component and full vehicle level. In full vehicle CFD models, vehicle package constraints of brake system within the wheel cavity is considered. Analyses are conducted for 3 different vehicle velocity conditions which are 30, 60 and 70 km/h. Component level CFD simulation correlation is targeted by measuring the rotor cooling duration on the inertia dynamometer to minimize the inertia dynamometer test effort during new rotor development.
EuroBrake 2021
POS
Downloads
Error message goes here.
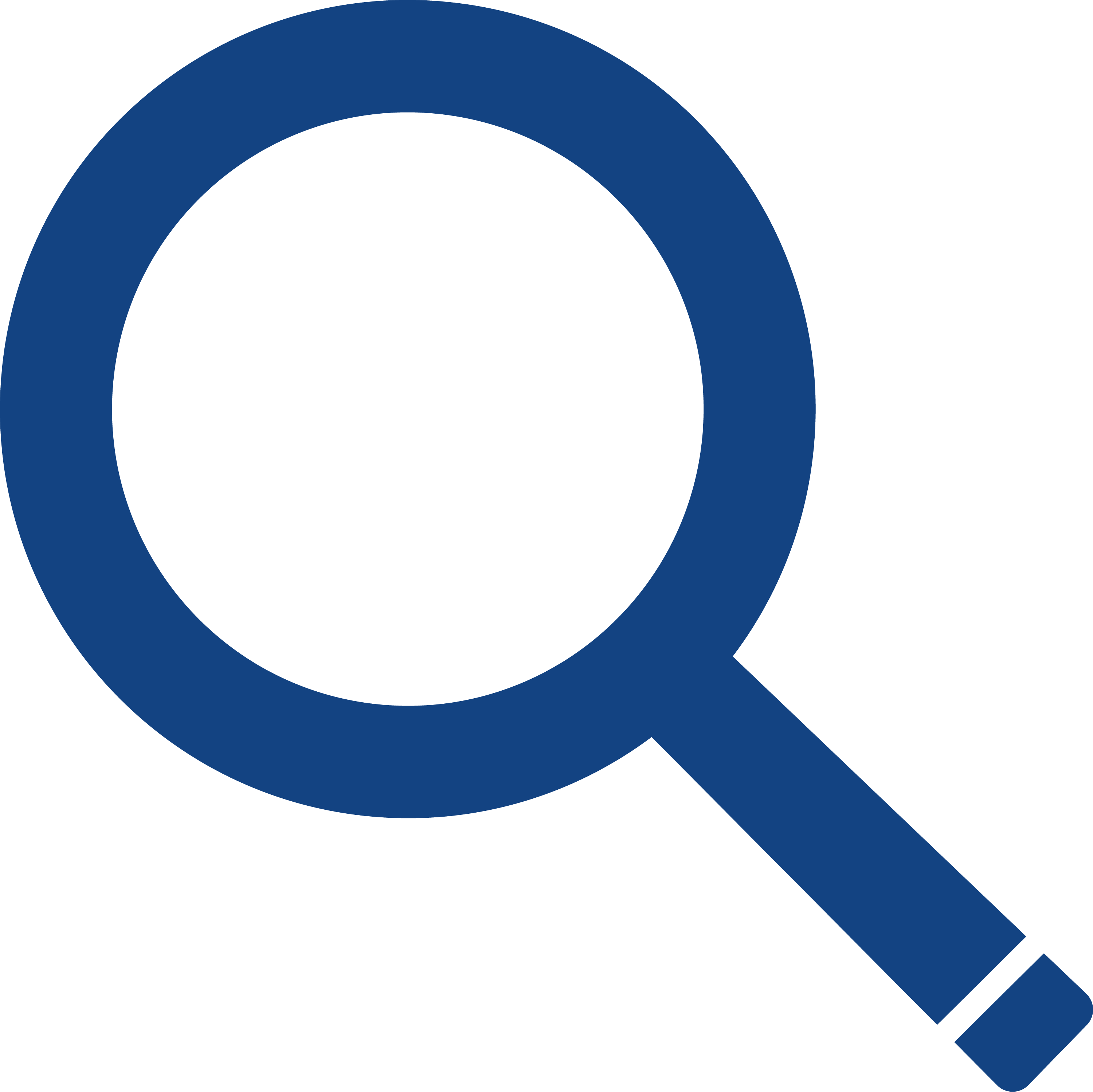
Person profile goes here.
Turkey
Ms. Dilek Bayrak Akça
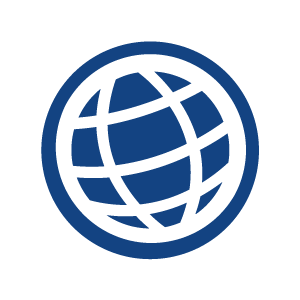
FISITA Committees & Groups
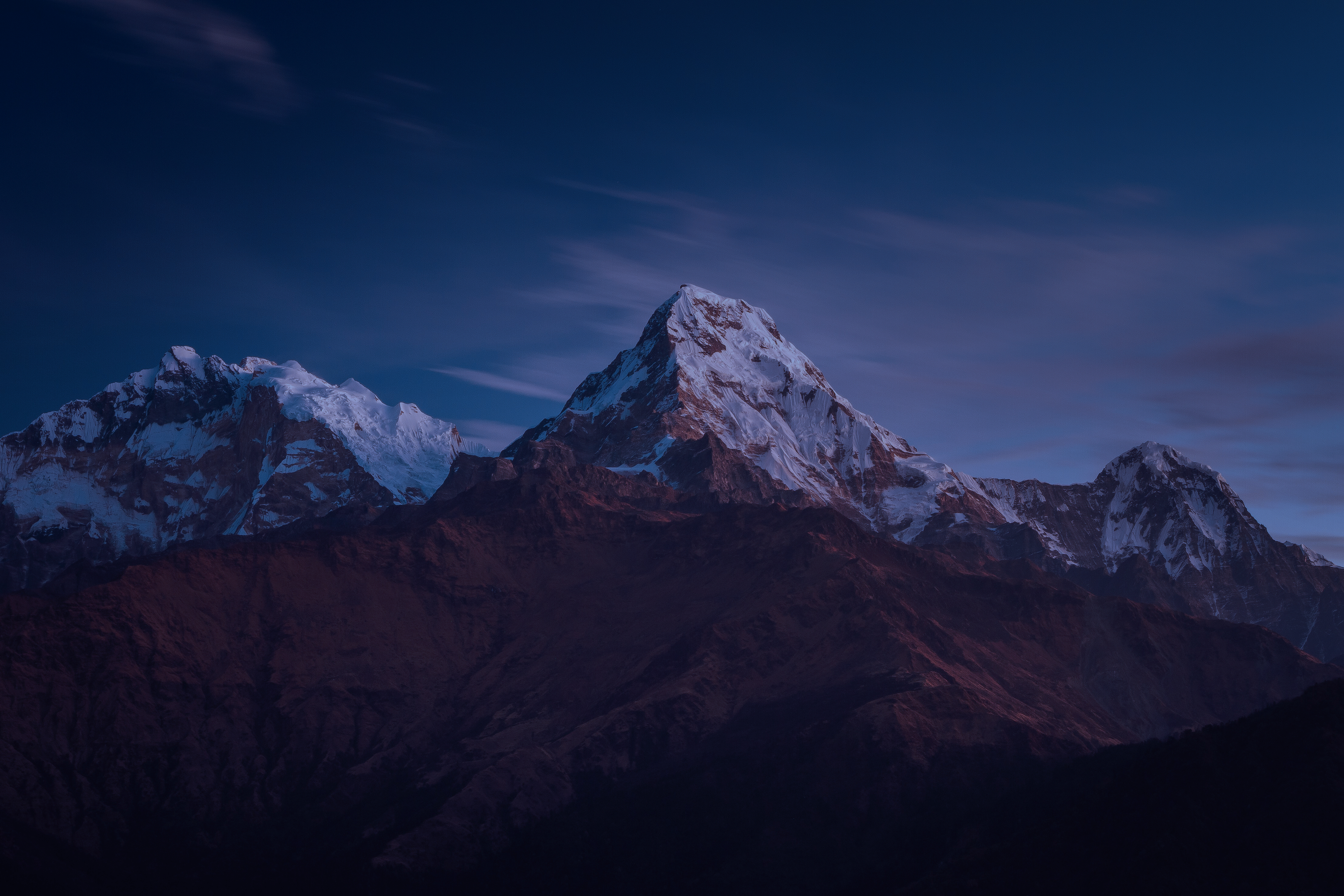