See FISITA Library items from Thilo Krah-Tomala
EB2021-MDS-003
Paper + Video + Slides
Abstract
Dr. Eng. Hossein Najafi, Oerlikon, SWITZERLAND
Ing. Cameron Eibl, Oerlikon, UNITED STATES
Ing. Franco Arosio, Oerlikon, GERMANY
Dr. Eng. Arkadi Zikin, Oerlikon, SWITZERLAND
Mr. Thilo Krah-Tomala, Oerlikon, GERMANY
The automotive industry is faced with a significant impending regulatory and environmental challenge: dramatically and cost effectively reduce brake dust emissions. To meet this challenge at scale, a high performing wear and corrosion resistant solution is needed that combines the advantageous economics of cast iron with a cost effective and indualizable coating. Alternative technologies such as composite brake discs are untenable for mass production, due to high costs and poor mass market value. The solution is to leverage Oerlikon’s patented and big data driven Rapid Alloy Design (RAD) platform to engineer disruptive new materials specifically tailored for the application and intended deposition methods.
Oerlikon has recently developed two new materials using the RAD platform balancing the corrosion, wear, mechanical, substrate, manufacturing, cost, and environmental parameters demanded by the brake disc application. This development leveraged two promising and industrialized deposition methods, extra high-speed laser cladding (EHLA) and high velocity oxygen fuel (HVOF) thermal spray. From a performance standpoint, the materials combine high corrosion performance and high wear resistance in a crack free solution. The materials are manufactured using low cost conventional atomization techniques and deposited as a single layer coating, significantly reducing processing costs. Environmental constraints are incorporated into the material design by eliminating carcinogenic Cobalt, Nickel, and Copper.
This article communicates the latest results on the deposition and performance of the new materials on brake discs using EHLA and HVOF technologies.
EuroBrake 2021
ACB
Downloads
Error message goes here.
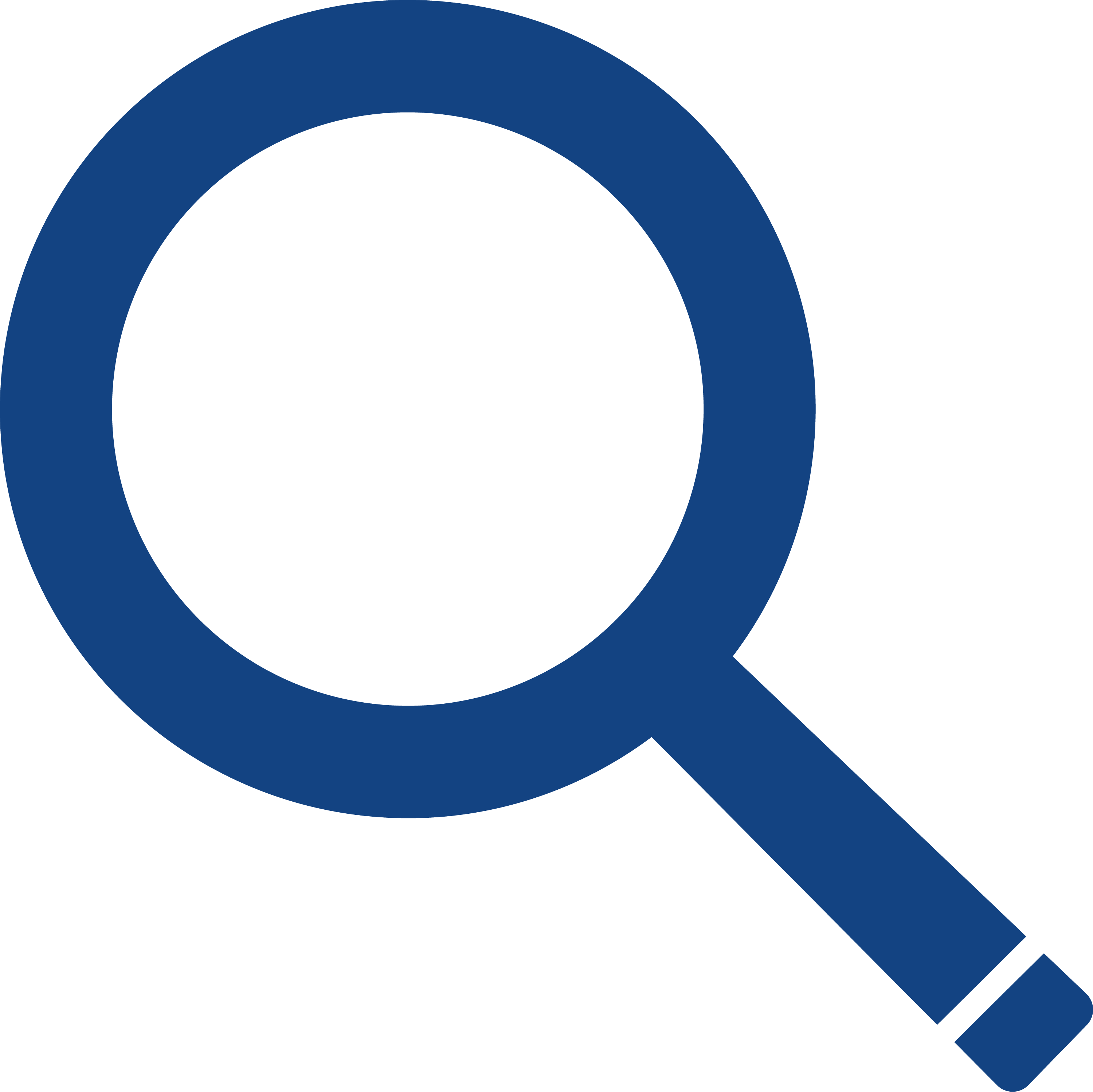
Person profile goes here.
Germany
Mr. Thilo Krah-Tomala
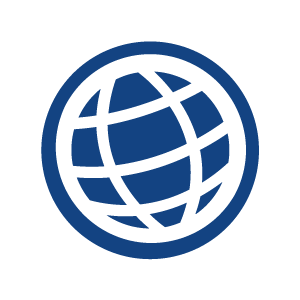
FISITA Committees & Groups
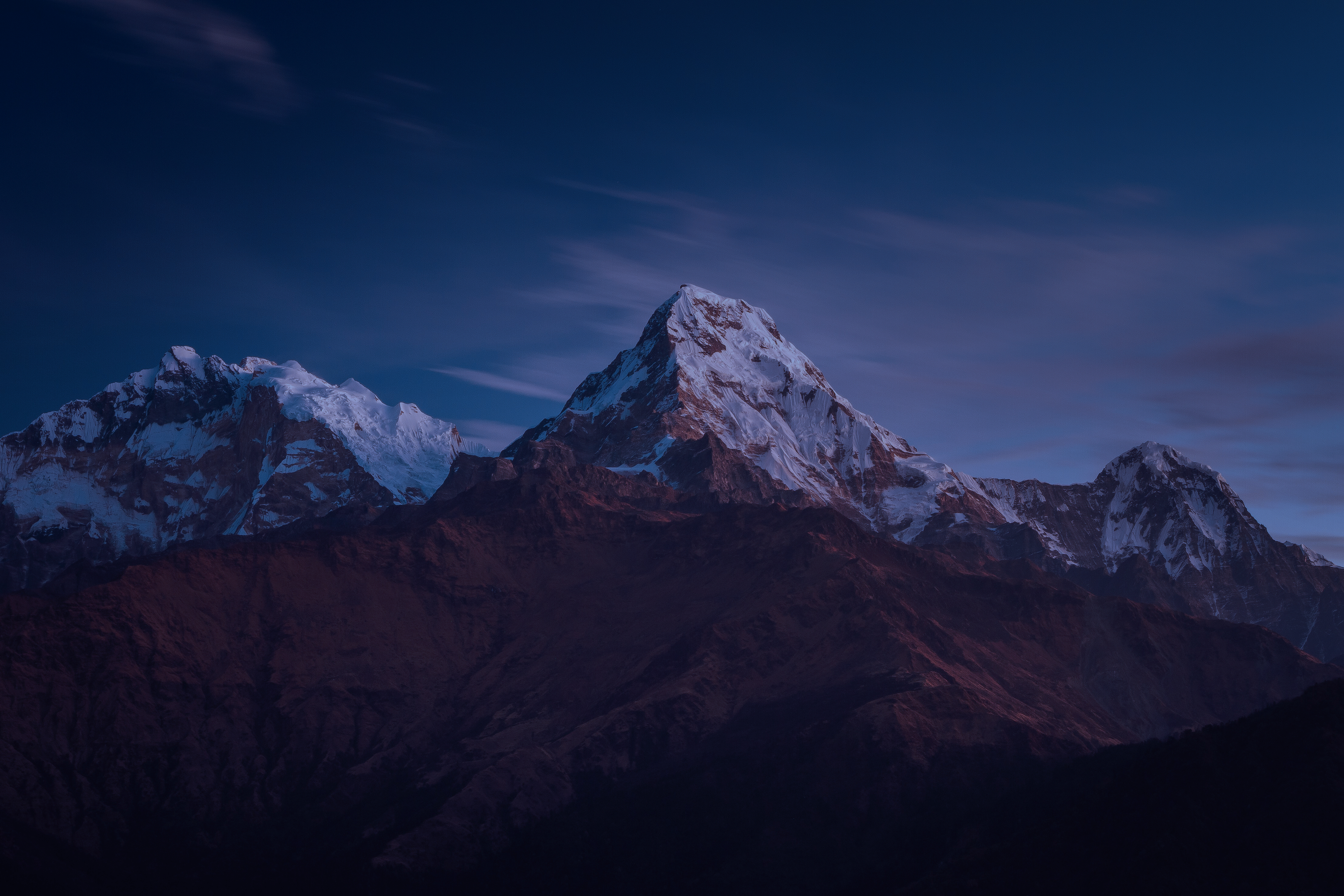