CO2 Foot Print Reduction in Brake Pad Industry
- FISITA
- Apr 20, 2021
- 2 min read
Name: Karsten Fischer
Company: Fischer Consulting
Presentation Title: CO2 Foot Print Reduction in Brake Pad Industry (EB2020-MFM-004)
Session: Advanced Manufacturing and CO2 Mitigation, Monday 17 May 2021, 12:00 - 13:40 (Central European Summer Time - CEST)
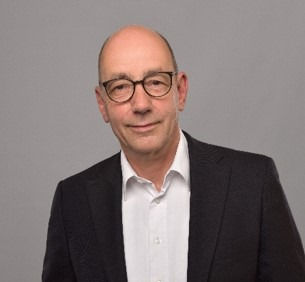
What do you find most interesting about the topic of your presentation?
Climate change is a reality and represents a challenge both for our generation as well as future generations. The temperature increase can only be limited to between 1.5 and 2.0 K if all areas of life are further developed:
Residential
Power generation
Traffic
Industry
Scientists and engineers of all disciplines must develop new methods for energy saving as well as regenerative energy production.
The brake pad industry must also face this challenge.
When discussing this topic with industry peers, what question are you most frequently asked? How do you answer it?
Question:
Is it possible to change the manufacturing process to one with higher energy efficiency without affecting the quality of the products?
Answer:
The automotive industry has very high quality requirements in terms of safety, durability, convenience and environmental compatibility. I recommend developing new manufacturing processes and new products together as part of a customer project. This way, customers are involved and the implementation in a cross-functional team is assured.
Who do you think will be most interested in your presentation, and who would you most like to ask questions about it?
EU leaders have agreed an ambitious goal for cutting greenhouse gases by 55% by 2030.
The year 2030 is fast approaching. That is why I would like to draw the attention of decision-makers to this challenge and outline a possible path.
Question:
Have you already drawn up an action plan for your company?
If so, where do you see the bottleneck?
What specific topics or technology are you hoping to see in other presentations or in the exhibition?
The automotive industry is undergoing a technological shift from internal combustion engines to electric/hydrogen drive types. One of the advantages of the new drives is that braking energy (kinetic energy) can be stored regeneratively as electricity.
I am therefore interested in what technical requirements are placed on the friction brake system and the brake pads in this context.
I would like to try to find out whether brake pads can be produced using completely new manufacturing processes in the future.
Register for EuroBrake 17-21 May 2021 to see over 100 technical presentations and posters, access technical content and replay sessions for three months after the event, and network with the community in the online event platform.
About Karsten Fischer.
2017 Founding of FischerConsulting
Proprietor
Consultant office with focus on
friction material processing/manufacturing
until 2016 Federal-Mogul Motorparts
Friction Material division
Director
Process engineering and prototype production
Process engineer – 30 years of experience in friction material processing
Comprehensive experience in leading global/multifunctional teams
Business experience:
Define and introduce (chemical) standard manufacturing processes for friction material business
Manage prototype production to support core and application development
Enable flawless proto handover to mass production
Comentários